Agricultural Start-Up Evergrow Aims To Develop Small Scale Farmers
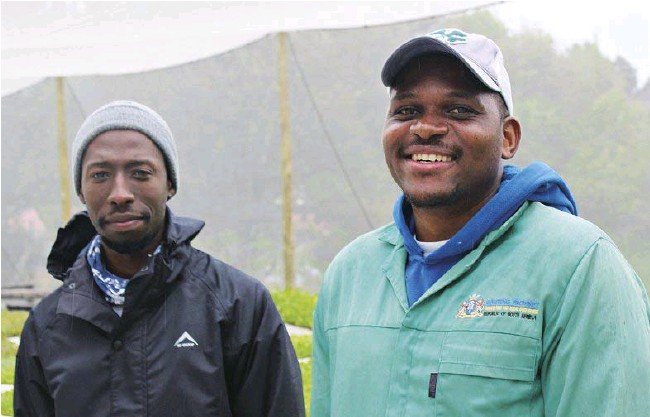
Agricultural Start-Up Evergrow Aims To Develop Small Scale Farmers. Evergrow (Pty) Ltd. is a South African Agricultural start-up focused on developing emerging small-scale farmers and youth skills within urban agricultural food value chains. The company understands productivity and sustainability are key challenges affecting small-scale farmers and agripreneurs in the country.
Co-founded back in 2018 by bio-scientists Andile Gcaza BSc. Biochemistry & Phetole Raseropo BSc. Botany. The company leverages in-house technical competences and experience to create an enabling environment for aspirant agripreneurs within the Horticultural Industry.
Evergrow has chosen to align with UN SDG 2 which seeks sustainable solutions to end hunger in all its forms by 2030 while achieving food security and poverty alleviation. The company believes by offering seedlings and primary consultation services to farmers it can increase production quantities, efficiency and quality of vegetable outputs, this then minimizes the planting and harvesting risks thus positively affecting incomes of small-scale farmers.
Evergrow Seedlings believes productivity and sustainability are key challenges affecting subsistence and emerging farmers, however through value added support such as capacity building workshops, masterclasses and extensive extension services cash-crop vegetable smallholders can adopt behavioral changes such as planting schedules as well as other risk mitigation strategies.
The dynamic duo are also graduates of Saica’s Enterprise Development (Saica ED) Flagship Programme which empowers SMMEs to elevate their businesses by offering them financial excellence through financial bootcamps, financial coaching, affordable accounting services, using accounting graduates where possible, and develop their financial excellence reporting standards. They established the business after identifying a gap within modern food systems around primary agricultural production value chains.