A First For Africa: Polyco Invests In New Recycling Technology – Converting Unrecyclable Plastic Into Eco-concrete
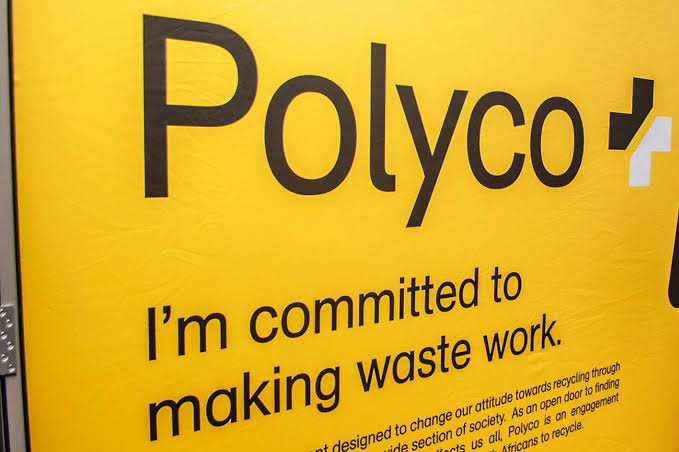
A First For Africa: Polyco Invests In New Recycling Technology – Converting Unrecyclable Plastic Into Eco-concrete. The plastic recycling sector has come a long way in South Africa with improved technology, better implementation of waste regulations, greater consumer awareness and growth in the market for recycled material. Despite these developments, there have always been plastic material streams that are difficult to recycle and therefore end up in landfill or, unfortunately, in the environment.
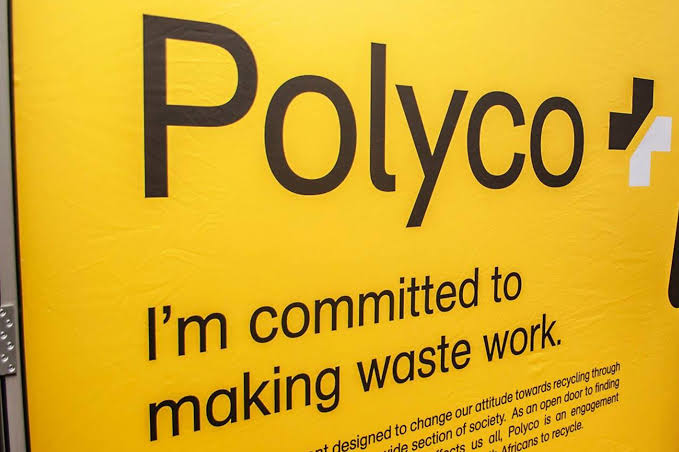
Seeking out a solution to repurpose unrecyclable and/or difficult to recycle plastic packaging, Polyco PRO NPC, a Producer Responsibility Organisation (PRO) in South Africa that represents and promotes the recycling of all plastic packaging, has provided a seven-million-rand, interest free loan to the Centre for Regenerative Design & Collaboration (CRDC) who will be using the funding to purchase machinery for their plant in Cape Town that converts unrecyclable and/or difficult to recycle plastic into eco-aggregate, that is then used in the building and construction sector. CRDC has designed an innovative solution that uses commonly mismanaged plastic waste and converts it to an eco-aggregate called RESIN8. Through various initiatives and collection schemes, CRDC accepts all plastics. The production of RESIN8 therefore contributes to increased recycling rates in South Africa and creates an output product that meets the acceptable building standards and is welcomed by the construction sector.
“One of the greatest challenges of the plastics and recycling sector has been finding a solution to repurpose and to reintegrate difficult to recycle plastics into the economy,” says Patricia Pillay, Chief Executive Officer at Polyco. “Our focus is to make waste a valuable resource, keeping all plastics out of the environment through investing in recycling infrastructure. The CRDC’s RESIN8 solution will divert thousands of tonnes of plastic that would have gone to landfill, or have landed up in the environment, but will now instead supply the construction sector with a high-quality eco-aggregate to be used in the production of various concrete products.”
To produce RESIN8, waste plastic is first shredded and then mixed with mineral additives. The mixed material is fed through an extruder to produce RESIN8, which is then granulated into a concrete aggregate-like material. The RESIN8 granules are used as a replacement for natural aggregates in the concrete mix used in the production of multitude of concrete products. To date, RESIN8 has been used towards the construction of 700 houses in Costa Rica, and in South Africa three large scale residential buildings in Khayelitsha and about 2000-meters of roadside kerb and channels on various projects in Cape Town.
This RESIN8 plant in Cape Town will be the first of its kind in Africa, and only the third plant in the world. “Our goal is to complete the construction phase before the year-end and to be fully operational from March 2023,” says Abraham Avenant, Chief Executive Officer at CRDC South Africa. “Once operational the plant will be able to process 610 tonnes of plastic waste per month into RESIN8.” To test the viability of RESIN8 as a construction aggregate, multiple concrete manufacturers partnered with CRDC’s South African team to test RESIN8 in building blocks, maxi bricks, pavers, kerbs, channels, and concrete pipes. Using RESIN8 decreases weight, increases or maintains strength, and increases the thermal properties of concrete bricks and blocks which adds additional environmental benefits.
“The Cape Town RESIN8 plant has been designed to be scalable and we aim to increase our production to 1220 tonnes of plastic waste per month. Our ambition is to replicate the Cape Town RESIN8 plant in a further two cities before the end of 2023,” says Avenant.