10 Ways South African SMEs Can Implement Lean Management
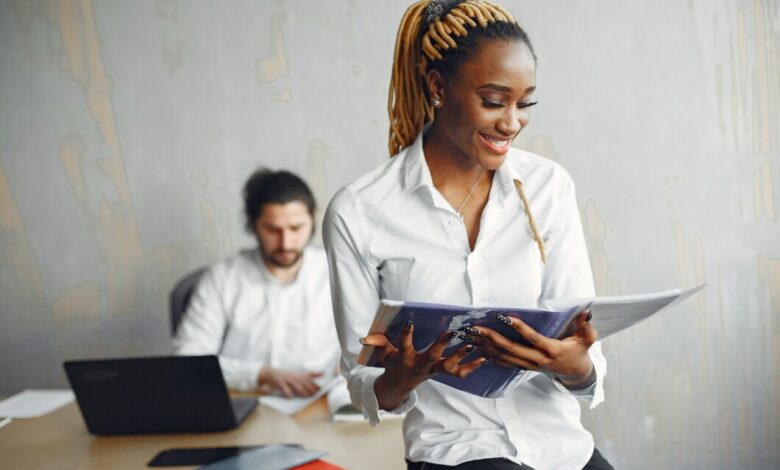
Lean management, which focuses on minimizing waste and maximizing value, can significantly enhance the efficiency and competitiveness of small and medium-sized enterprises (SMEs) in South Africa. Here are ten practical strategies for implementing lean management in South African SMEs:
1. Identify and Eliminate Waste
The first step in lean management is identifying and eliminating waste in all its forms—whether it’s time, resources, or materials. SMEs should conduct a thorough analysis of their processes to identify any non-value-adding activities. Common types of waste include overproduction, excess inventory, waiting times, unnecessary transportation, and defects. By streamlining operations and focusing on value-adding activities, SMEs can reduce costs and improve efficiency.
2. Adopt a Continuous Improvement Mindset
Continuous improvement, or Kaizen, is a core principle of lean management. It involves making small, incremental changes regularly to improve processes. SMEs should encourage employees at all levels to suggest improvements and participate in problem-solving activities. Establishing a culture where continuous improvement is valued can lead to significant long-term benefits.
3. Implement 5S Methodology
The 5S methodology—Sort, Set in Order, Shine, Standardize, and Sustain—is a simple yet effective way to organize and maintain a productive workplace. By implementing 5S, SMEs can improve efficiency, reduce waste, and create a safer working environment. Regular audits and employee involvement are crucial to sustaining the benefits of 5S.
4. Streamline Communication
Effective communication is vital for lean management. SMEs should ensure that information flows smoothly across all levels of the organization. This can be achieved through regular meetings, clear documentation, and the use of digital tools to facilitate communication. Transparent and open communication helps in quickly identifying and addressing issues, fostering a collaborative environment.
5. Empower Employees
Lean management emphasizes the importance of employee involvement and empowerment. SMEs should provide training and development opportunities to equip employees with the skills needed to identify and solve problems. Empowering employees to make decisions and take ownership of their work can lead to more efficient and innovative solutions.
6. Focus on Customer Value
Understanding and delivering what customers value is central to lean management. SMEs should engage with their customers to gather feedback and insights on their needs and preferences. By aligning their processes and products with customer expectations, businesses can enhance customer satisfaction and loyalty.
7. Utilize Visual Management
Visual management tools, such as charts, dashboards, and visual controls, can help SMEs monitor performance and identify issues quickly. These tools make it easier for employees to understand and engage with key metrics, fostering a culture of accountability and continuous improvement.
8. Optimize Inventory Management
Effective inventory management is crucial for reducing waste and improving cash flow. SMEs should implement just-in-time (JIT) inventory systems to reduce excess stock and minimize storage costs. By maintaining optimal inventory levels, businesses can respond more flexibly to customer demand and reduce the risk of obsolescence.
9. Standardize Work Processes
Standardizing work processes ensures consistency and quality in operations. SMEs should document best practices and establish standard operating procedures (SOPs) for critical tasks. Standardization reduces variability, making it easier to identify deviations and implement improvements.
10. Measure and Analyze Performance
Regularly measuring and analyzing performance is essential for lean management. SMEs should identify key performance indicators (KPIs) that align with their goals and track them diligently. Using data analytics, businesses can gain insights into their operations, identify trends, and make informed decisions to drive continuous improvement.
Implementing lean management can transform South African SMEs by enhancing efficiency, reducing costs, and improving customer satisfaction. By focusing on waste elimination, continuous improvement, employee empowerment, and data-driven decision-making, SMEs can build a competitive advantage and achieve sustainable growth. Adopting these lean principles and strategies will enable South African SMEs to navigate challenges and thrive in an increasingly competitive market.